Automated high-bay warehouse with AGVs: Future-proof logistics solutions for HIK.
The competitive pressure in the industry is continuously increasing, and HIK is also facing the challenge of continuously optimizing its processes. Especially in the field of logistics, efficiency and flexibility are crucial factors that can determine the success of a company.
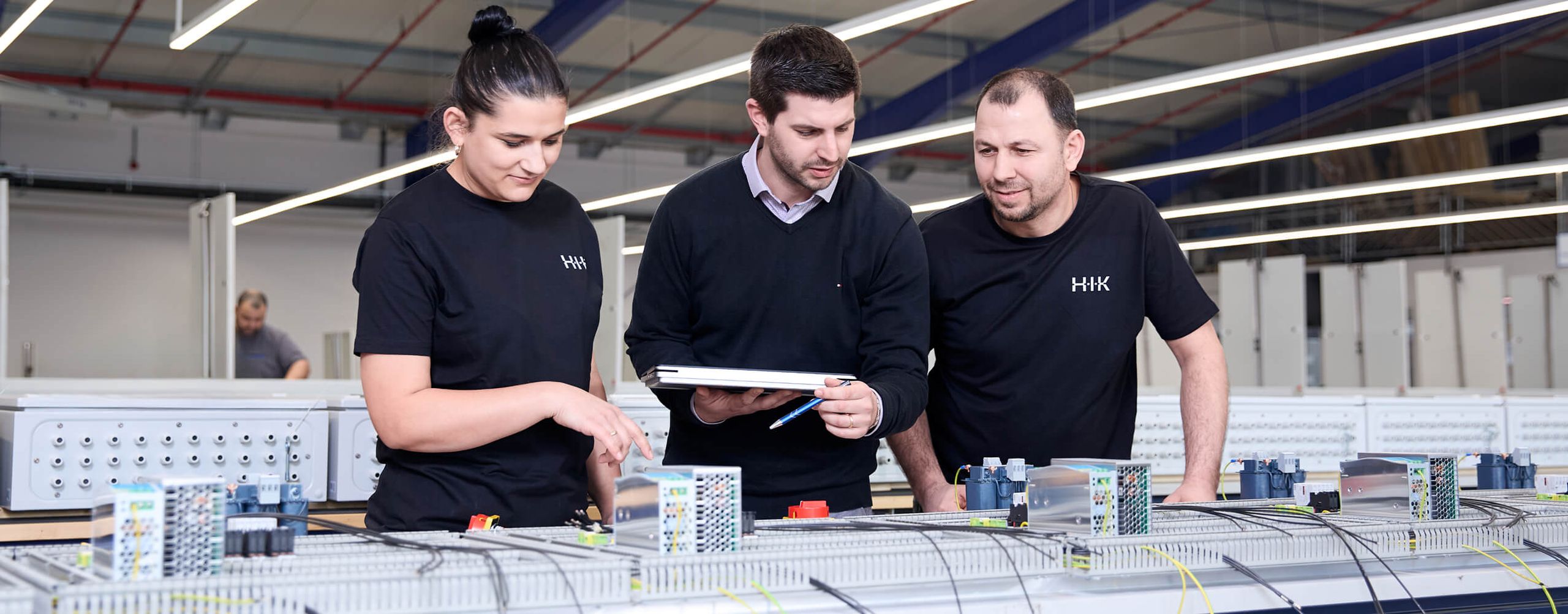
In this context, HIK has opted for a future-proof complete solution that meets the requirements of modern manufacturing and at the same time makes a significant contribution to process optimization.
In order to optimize the logistics processes, a state-of-the-art, fully automated high-bay warehouse with 3,000 pallet spaces has been put into operation. Together with several driverless transport systems (FTS), this ensures efficient material supply to the various production areas. The core task of the system is the complete automation of goods storage, provision, and retrieval.
Automation starts already with the storage of pallets: Two driverless narrow aisle forklifts take care of storing and retrieving the pallets in the high-bay warehouse. Once the pallets are stored in the respective shelves, driverless pallet trucks take over the transportation of the materials and bring them to the production areas where they are needed. After the material has been used, automatic return and re-storage take place.

Material provision around the clock
The modern ERP system ensures that materials are provided on a job-related and demand-oriented basis - around the clock, 7 days a week, 365 days a year. This continuous provision ensures uninterrupted production and minimizes downtime that could be caused by missing materials. Human errors that occur in manual warehouse processes are reliably eliminated by the fully automated solution. The result: no shortages or excess inventory, and no unnecessary production interruptions.
The driverless transport systems (FTS) are equipped with advanced laser environment detection, allowing them to move safely and flexibly through various manufacturing areas. The system reacts adaptively to potential obstacles, avoiding traffic jams and delays, ensuring that material provision is always quick and smooth. This also helps prevent and reduce accidents and damage to goods or infrastructure. Real-time tracking enables employees to track the location of materials at any time, ensuring even better control over the entire process.
Another advantage of the automated high-bay warehouse is the relief of employees in logistics. Instead of dealing with physically demanding and repetitive tasks such as lifting and transporting pallets, they can now take on value-added activities. This improves the quality of work while minimizing health risks.
A particularly noteworthy feature of the new system is its flexibility: The high-bay warehouse and the driverless transport systems can be expanded at any time with additional AGVs and pallet spaces. This scalability ensures that HIK can keep up with the increasing demands and the growth of the company in the future.